Course Information
Lean for Support Processes Training
Learners will be able to:
- Apply Lean practices to office/business support processes.
- Translate the Seven Wastes to apply to office/business support processes.
- Use Lean techniques to reduce waste and streamline office systems.
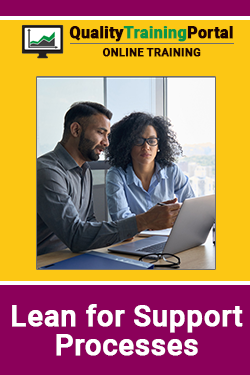
About This Course
How can Lean Concepts Apply in Non-Manufacturing?
Lean manufacturing has been used both conceptually and in practice to identify and eliminate waste in manufacturing operations for years. Can Lean Manufacturing principles and practices be applied to business processes? Of course! Lean is all about getting waste out of processes and waste isn’t just something that happens in manufacturing. Non-manufacturing processes have hand-offs, disconnects, incomplete communications and rework loops. Office and support processes are often ripe for streamlining and many of the same improvement tools such as process mapping, the 5S’s, and error-proofing can be used to achieve significant efficiencies. Lean process measures can then be put into place to monitor the improvement results, hold the gains and identify new opportunities for improvement.
Lean for Support Processes Online Training
Lean for Support Processes online training is designed specifically for those working in business processes and transactional environments. The course begins with explanations and examples of the Seven Wastes in “office-friendly” terms. Process mapping techniques are coupled with process streamlining methods to demonstrate how value streams can be configured to be more effective. The course adds 5S, error-proofing and TPM techniques to the Lean Business Process arsenal and wraps up with descriptions of measures that can be used to sustain and expand the Lean initiative. We also have a Lean Manufacturing course for manufacturing environments.