Course Information
AIAG-VDA Process-FMEAs Training
Learners will be able to:
- Participate as a core member of an AIAG-VDA Process-FMEA Team.
- Rate the risk of potential failure modes using Action Priority Levels.
- Develop action plans to address risks that are unacceptably high.
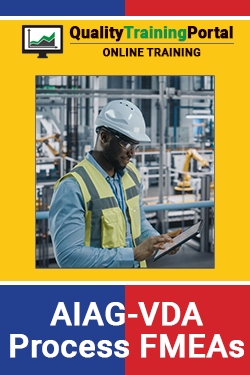
About This Course
Failure Mode and Effects Analysis (FMEA) techniques have been used for over 70 (yes, SEVENTY!) years. In recent years, use of FMEAs has gained popularity as a quality improvement tool. Most industries are now using FMEA techniques as part of their risk assessment and risk mitigation strategies. Unlike many quality improvement tools, FMEAs do not require complicated statistics yet they can yield significant savings for a company as well as reduce potential risks and associated liabilities of a product or process that does not perform as intended.
In 2019, AIAG (Automotive Industry Action Group, www.aiag.org) and VDA (Verband der Automobilindustrie, www.vda.de), two of the leading automotive trade associations, unveiled a major revision to FMEA methodology with the release of the AIAG-VDA FMEA Handbook.
This online training prepares learners to participate on the core team of a Process-FMEA (PFMEA) using the 2019 AIAG-VDA FMEA Process. The course provides a background understanding of FMEAs including their history, detailed instruction on how to use the seven-step FMEA process and highlights tips for getting the most out of PFMEAs.
IMPORTANT NOTE: While the AIAG-VDA Process-FMEAs course is in line with the AIAG-VDA FMEA Handbook, it is not intended as a replacement for the source Handbook. We recommend that this course be used in conjunction with the official Handbook.
- None.
- English (EN-US)
- Chinese (simplified) (ZH)
- Czech (CS)
- French (FR)
- German (DE)
- Italian (IT)
- Japanese (no audio) (JA)
- Korean (no audio) (KO)
- Polish (PL)
- Portuguese (Brazilian) (PT-BR)
- Romanian RO)
- Russian (RU)
- Spanish (ES)
- Vietnamese (no audio) (VI)
Course Objectives
- Describe the systematic approach that FMEAs take to identify and reduce risks.
- Compare and contrast the different types of FMEAs and describe the relationship between DFMEAs and PFMEAs.
- Define what the Five T’s are and explain how they are used to ensure successful FMEA team start-ups.
- Learn to use the Seven-Step AIAG-VDA PFMEA process.
- Describe the “Failure Chain” concept in FMEAs.
- Understand how evaluation criteria is used to rate the levels of Severity, Occurrence and Detection and how the S-O-D rating is used to establish the Action Priority Level of potential failure modes.
Course Outline
Lesson 1 | Why Conduct PFMEAs?
- Know what an FMEA is and why an FMEA is used.
- Understand how an FMEA is conducted on a conceptual basis.
Lesson 2 | Brief History of FMEAs
- To gain an appreciation of the historical evolution of FMEAs, the types of FMEAs that are used and the industries that use them.
Lesson 3 | Overview of the PFMEA Process
- To understand the scope and scale of the seven-step PFMEA process.
Lesson 4 | System Analysis (Steps 1, 2 & 3)
- To appreciate how to charter and start-up a PFMEA team.
- To understand how to analyze the structure of the process under study.
- To learn how to identify the functions of each process step.
Lesson 5 | Failure Analysis and Risk Mitigation (Steps 4, 5 & 6)
- To understand the concept of a Failure Chain.
- To use the Failure Chain model to identify failure modes, failure effects and failure causes for each process step.
- To realize how to use Evaluation Criteria to rate the Severity, Occurrence and Detection for each failure.
- To understand how to create custom Evaluation Criteria.
- To learn how to use the Action Priority Tables to assign AP Levels.
- To use common problem-solving tools to develop risk mitigation plans.
Lesson 6 | Communication (Step 7)
- To know how to document and communicate PFMEA results.
Lesson 7 | Helpful Tips
- To be aware of approaches that can help teams conduct PFMEAs more effectively and efficiently.
Challenge
- An assessment of the learner’s progress in this course.
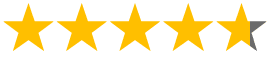
4.7 out of 5 stars
Comments from Learners About This Course
- The training is very useful, it did help me to get a better understanding towards PFMEA. Very Helpful.
- Good course. Detailed and good examples.
- Detailed and organized training material. Easy to understand, interesting and informative.
- Very thorough and really helped me get a handle on some of the new ways of thinking about how to perform a PFMEA using the AIAG-VDA approach.
- It’s great at how much it goes down to details.
- The course is comprehensive and well organized.
- Great tool and in specific for VDA-FMEA was really clear to understand the application and implementation, I was using only the AIAG book but this training was super clear to follow up. Thanks!!!
- Great questions that really make you embed the information into your mind.
- Thank you for this helpful training, this is an important part of my job and these updates are really concrete and well structured.
- The a great way to learn about the PFMEA new methodology. Thanks.
- The approach is good….tell ’em you’re gonna tell ’em, tell ’em, and tell ’em you told ’em.
You may also be interested in…
- Mistake-Proofing Training – Comprehensive online training in poka yoke/mistake-proofing techniques for manufacturing operations.
- 8D Problem-Solving – Step-by-step training in how to work on a problem-solving team follow the 8D methodology including tools and techniques that are used in each step.
- Root Cause Analysis with Corrective Action – Leads the learner through a four-step process to get to the root cause (source) of problems to eliminated problems for good.