Course Information
Basic SPC Training
Learners will be able to:
- Measure and analyze process variation pictorially and using simple statistics.
- Use control charts to monitor process variation.
- Understand fundamental concepts of process capability.
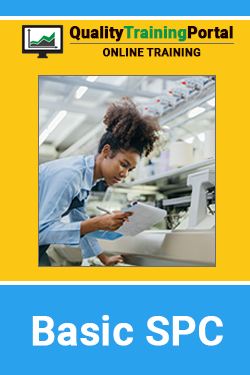
About This Course
SPC or statistical process control is a statistically-based family of tools used to monitor, control, and improve processes. Statistical Process Control (SPC) training can be time-consuming and frustrating because of the complex nature of the statistics underlying SPC control charts. Basic SPC is a comprehensive online SPC training course for engineers, operators, and technicians that makes understanding and applying statistical process control (SPC) concepts easy.
With Basic SPC online SPC training, you can eliminate or substantially reduce the need for expensive and inflexible classroom training. In addition to providing a solid understanding of variation and the statistics upon which control charts are based, this course covers the use of the most common variable and attributes control charts including x-bar & R-charts, moving average charts, p-charts, u-charts, np charts, and c charts.
Extensive training includes collecting sample subgroups, plotting points on control charts, and interpreting SPC charts. This online basic SPC training course also features a conceptual overview of process capability including Cp, Cr, and Cpk to provide learners is a well-rounded and thorough understanding of how to use statistical process control in their jobs. This training is ideal for Six Sigma Green Belt training or for lean manufacturing training.
- Basic math skills.
- English (EN-US)
- Chinese (simplified) (ZH)
- Czech (CS)
- French (FR)
- German (DE)
- Italian (IT)
- Japanese (no audio) (JA)
- Korean (no audio) (KO)
- Polish (PL)
- Portuguese (Brazilian) (PT-BR)
- Romanian RO)
- Russian (RU)
- Spanish (ES)
- Vietnamese (no audio) (VI)
Course Objectives
Unit 1 | Understanding Variation
- Explain what variation in a work process is and why it is bad.
- Describe key techniques for measuring variation – visual display and mathematical.
- Identify key patterns of variation and explain what causes them.
Unit 2 | Using Control Chart
- Understand the purpose of a control chart.
- Identify key parts of a control chart.
- Know how to collect and plot data on a control chart.
- Be able to interpret and take action using a control chart.
Unit 3 | Process Capability Basics
- Describe what is meant by a capable process.
- Contrast the difference between an “in-spec” process and a “capable process.”
- Identify and explain the three main measures of process capability.
Course Outline
Unit 1 Understanding Variation
Lesson 1 | Introduction to Variation
- What variation is and why it’s a problem in manufacturing.
Lesson 2 | Measuring Variation
- Using a histogram to measure the variation in a process.
Lesson 3 | Patterns of Variation
- Types of patterns of variation, what they tell you, and what to do about them.
Lesson 4 | Measures of Variation
- Statistical measures of variation: Mean, range, and standard deviation.
Lesson 5 | Normal Curve
- Properties of the normal curve and the 68, 95, 99.7 rule.
Lesson 6 | Stability
- The importance of a stable process in manufacturing.
Unit Challenge
- An assessment of the learner’s progress in this unit.
Unit 2 Using Control Charts
Lesson 1 | What are Control Charts
- What control charts are and why they are used.
Lesson 2 | What a Control Chart Looks Like
- Common elements of all control charts.
Lesson 3 | Interpreting Control Charts & Taking Action
- Out-of-control patterns and what to do when they occur.
Lesson 4 | Types of Control Charts
- Variable and attribute control charts: Which do you use when?
Lesson 5 | Using Variable Control Charts
- Calculating and plotting data on variable control charts and interpreting the chart.
Lesson 6 | Using Attribute Control Charts
- Calculating and plotting data on attribute control charts and interpreting the chart.
Unit Challenge
- An assessment of the learner’s progress in this unit.
Unit 3 Process Capability Basics
Lesson 1 | What is Process Capability
- What process capability means and why it’s important.
Lesson 2 | Measuring Process Capability
- The capability ratio, process capability index, and Cpk.
Unit Challenge
- An assessment of the learner’s progress in this unit.
4.6 out of 5 stars
Comments from Learners About This Course
- I really enjoyed the course. The information will be very valuable to our plant in the near future.
- Gave a good insight into SPC.
- Quick and concise! Easy to follow and good use of the challenges to ensure you understand all material covered in the course.
- Course was very informative. It was a refresher course for me and I must say I needed some of the information. Thank you.
- Very interesting, and eye-opening.
- Very complete, and takes you step by step to understand the basics of SPC.
- This course is very good. I learned a lot about quality control.
- Great Course, lots of examples to help with the explanations of the material.
- Course material covered a wide range of topics and examples were useful to describe this in “real-terms.” The test questions covered the range of topics
You may also be interested in…
- Advanced Control Charts – Step-by-step training in how to set up a variety of different control charts as well as how to determine the best chart to use in given situations.
- Advanced Process Capability – Step-by-step training in how to conduct a process capability study as well as how to handle process capability study complications.
- Mistake-Proofing Training – Comprehensive online training in poka yoke/mistake-proofing techniques for manufacturing operations.
- 8D Problem-Solving – Step-by-step training on how to work on a problem-solving team following the 8D methodology including tools and techniques that are used in each step.