Course Information
Advanced Product Quality Planning Training
Learners will be able to:
- Use the NEW 2024 APQP Guidelines (following the AIAG 3rd Edition Reference Manual) when designing and developing new products.
- Apply quality improvement tools and techniques throughout the APQP process.
- Explain how PPAP is used to communicate product quality status to customers.
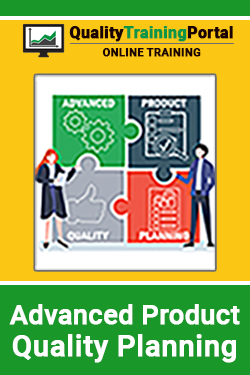
About This Course
The Advanced Product Quality Planning course consists of seven lessons and a self-assessment test (called a Challenge.)Â This Reference Guide recaps the key points of the content for the course.
The initial lesson provides an overview of the APQP process, focusing on Phase 0: Preparation (Program Concept and Initiation Phase). The next five lessons cover the five primary phases of APQP, and the final and last lesson recaps the full process.
APQP stands for Advanced Product Quality Planning. The Automotive Industry Action Group (www.aiag.org) developed the methodology. Note: Our course is intended as a supplement, not a replacement, for the AIAG APQP Reference Manual, Third Edition.
The Advanced Quality Planning Process was originated to provide a common, standardized process for planning, developing, and communicating the requirements and status of new products and services between suppliers and their customers. The Advanced Product Quality Planning course is intended to help practitioners understand the APQP process and apply it to the development of new products and their corresponding processes.
- Mistake-Proofing or Error-Proofing or the equivalent understanding of the difference between fixing problems after they happen and preventing problems from happening in the first place.
- English (EN-US)
- Chinese (simplified) (ZH)
- Czech (CS)
- French (FR)
- German (DE)
- Italian (IT)
- Japanese (no audio) (JA)
- Korean (no audio) (KO)
- Polish (PL)
- Portuguese (Brazilian) (PT-BR)
- Romanian RO)
- Russian (RU)
- Spanish (ES)
- Vietnamese (no audio) (VI)
Course Objectives
- Explain the purpose of the APQP process and use the sequential phases of the APQP process.
- Be aware of techniques used to identify the VOC (Voice of the Customer.)
- Understand how Design-FMEAs can help reduce risks in the design phase and Process-FMEAs can help reduce process related risks.
- Be familiar with a Design Verification Plan and Report.
- Understand the progress of Control Plans from Prototype to Pre-Launch to Production Phases.
- Understand how Engineering Change Requests generate vital documentation.
- Be familiar with the Production Part Approval Process (PPAP).
- Know about tools and techniques that are used to continuously improve both the product and its corresponding process.
- Be aware of the Gated Management process, which requires leadership to sign off on each APQP phase before it is considered complete.
Course Outline
Lesson 1 | Overview of APQP
- Explain the purpose of the APQP process.
- Describe the five phases of the APQP process.
- Understand the steps necessary to prepare for APQP
Lesson 2 | Phase 1: Plan and Define
- Describe the purpose and objectives of Phase 1.
- Explain how customer needs and expectations can be translated into a value-added (and competitive) offering.
- Become familiar with the design, reliability and quality goals of Phase 1.
Lesson 3 | Phase 2: Product Design and Development
- The design of the product is fleshed out.
- After the design is verified, a prototype is built, specifications developed and inputs for the process design are generated.
Lesson 4 | Phase 3: Process Design and Development
- Describe how the conceptual product direction from Phase 1 is formalized into a detailed design.
- Become familiar with how compiled outputs of Phase 2 become the foundation for a comprehensive design of the process.
Lesson 5 | Phase 4: Product and Process Validation
- Describe the information and data needed to develop a detailed design of the process.
- Become familiar with how the detailed process design will set the stage for product and process validation.
Lesson 6 | Phase 5: Feedback Assessment & Corrective Action
- Describe how inputs are collected and complied for improving the product and process.
- Explain techniques reducing common cause variation, addressing customer satisfaction issues, improving delivery and service issues and applying lessons learned.
Lesson 7 | Recap of the APQP process
- Review a summary of the major elements and benefits of the APQP process.
Challenge
- An assessment of the learner’s progress in this course.

4.5 out of 5 stars
Comments from Learners About This Course
- Very Nice Course. All material is explained in very simple manner.
- Excellent overall view of the APQP Process.
- This class was fantastic!
- Amazing Training. Congratulations QualityTrainingPortal.
- Great course that provides a clear overview of APQP process!
- Very good .. filled all knowledge gaps.
You may also be interested in…
- PPAP Training – A Targeted Training Course on the Production Part Approval Process.
- Advanced SPC Training – Comprehensive training in how to implement statistical process control including setting up control charts and conducting process capability studies.
- FMEA Training – Complete online training in how to conduct Design and Process FMEAs and to reduce high Risk Priority Numbers, how to customize FMEAs for a specific business and how to maintain improved processes using a control plan.
- Measurement Systems Analysis – Comprehensive training in how to statistically measure the accuracy and reliability of measurement systems.