Course Information
Lean for Job Shops Training
Learners will be able to:
- Explain why many traditional Lean techniques do not work in a Job Shop.
- Implement Lean techniques are best suited for Job Shops.
- Develop a plan for rolling out Lean in a Job Shop.
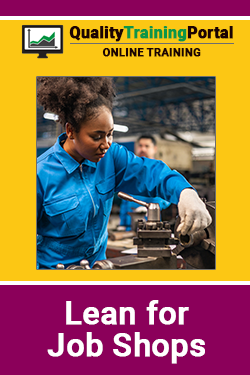
About This Course
How can Lean Concepts Apply in Job Shops?
For years, Lean practices have helped manufacturing operations reduce waste and improve operational effectiveness. Unfortunately, some Lean tools and techniques do not translate well to Job Shop operations. Since Job Shops deal with an unpredictable and diverse product mix of short runs, some cornerstone Lean tools are not practical. Value Stream Mapping does not yield the same insight for a high-mix, low-volume operation as it does for a low-mix, high-volume process. Likewise, takt time, line balancing and even full adoption of flow cells are not as important in a Job Shop environment as they are in high-volume operations.
Does this mean that Lean Manufacturing has no place in a Job Shop? Absolutely not! Many conventional Lean practices can be adapted for use in a Job Shop and can produce the same level of waste reduction and value-added gains as can be generated in high-volume, low-mix processes.
Lean for Job Shops Online Training
Lean for Job Shops online training is designed specifically to help Job Shops adapt, prioritize and apply Lean Manufacturing tools and techniques to a Job Shop environment. Participants will learn how to implement Lean Manufacturing practices to complement the realities of their unique job shop environment.
The Lean for Job Shops online training has two units. Unit 1, Adapting Lean to Job Shops, starts by exploring the “Realities of Job Shops,” the related consequences to the operation and outlines a three-phased approach to address the “realities.” In Unit 2, Lean Job Shop Practices, five significant action plans for a Lean Job Shop environment are presented as a series of interdependent activities. These, coupled with trend analysis measures, will lead to success in making Job Shops lean and (more) productive.
- An understanding and application of the principles of the 5S’s such as Introduction to the 5S’s or equivalent.
- English (EN-US)
- Chinese (simplified) (ZH)
- Czech (CS)
- French (FR)
- German (DE)
- Italian (IT)
- Japanese (no audio) (JA)
- Korean (no audio) (KO)
- Polish (PL)
- Portuguese (Brazilian) (PT-BR)
- Romanian RO)
- Russian (RU)
- Spanish (ES)
- Vietnamese (no audio) (VI)
Course Objectives
Unit 1 | Adapting Lean to Job Shops
- Realize that Lean approaches can be modified and adapted to deal with Job Shop Realities.
- Define key Lean manufacturing terms.
- Describe vital Lean tools.
- Be familiar with additive Lean techniques.
- Identify the Seven Wastes and briefly describe how each of the Seven Wastes detracts from the value of a process’ output
- Uncover patterns of how the effects of Job Shop Realities lead to Waste.
- Understand that Lean practices can be adapted to a Job Shop environment by developing a compelling Message, building Momentum and making structural changes (the Means.)
- Become aware that the Means can be a combination of the 5S’s, Set-up Reduction, Workflow/Layout adjustments, TPM and Visual Workplace practices.
Unit 2 | Lean Job Shop Practices
- Become familiar with how a three-phased approach (Message, Momentum and Means) can be used to adapt Lean practices and understand how the “Means” represent a series of interdependent action plans.
- Identify what each of the 5S’s stands for and how it helps an organization reduce waste.
- Identify the key components of set-up reduction and explain the role each plays in reducing set-up time.
- Understand the linkage between layouts and workflows and know how to adjust layouts to make workflows more effective.
- Know the difference between Corrective Maintenance, Preventive Maintenance (PM) and Predictive Maintenance (PdM) and how to incorporate appropriate maintenance practices to improve equipment reliability.
- Appreciate how powerful visual aids, supports and alerts can be incorporated to make it easier to do things the right way and reduce waste.
- Be able to use measures to track and evaluate Lean Job Shop action plans.
Course Outline
Unit 1 Adapting Lean to Job Shops
Lesson 1 | Does Lean Really Apply?
- Appreciate the Realities that Job Shops must contend with.
- Be aware of the consequences of those Realities.
- Realize that Lean approaches can be modified and adapted to deal with Job Shop Realities.
Lesson 2 | Lean Job Shop Terminology
- Define key Lean manufacturing terms.
- Describe vital Lean tools.
- Be familiar with additive Lean techniques.
Lesson 3 | Wastes in Job Shop Terms
- Identify the seven wastes.
- Explain value-adding versus non-value adding.
- Define value from the customer’s perspective.
- Briefly describe how each of the seven wastes detracts from the value of a process’ output.
Lesson 4 | Linking Realities to Wastes
- Associate Job Shop Realities with the Seven Wastes.
- Uncover patterns of how the effects of Job Shop Realities lead to Waste.
- Discover common themes of the effects and the corresponding impact on Waste.
- Recognize potential root causes of the common themes.
Lesson 5 | Preview of the Means
- Understand that Lean practices can be adapted to a Job Shop environment by developing a compelling Message, building Momentum and making structural changes (the Means.)
- Become aware that the Means can be a combination of the 5S’s, Set-up Reduction, Workflow/Layout adjustments, TPM and Visual Workplace practices.
Unit 1 Challenge
- An assessment of the learner’s progress in this unit.
Unit 2 Lean Job Shop Practices
Lesson 1 | Message, Momentum and Means
- Become familiar with how a three-phased approach (Message, Momentum and Means) can be used to adapt Lean practices to a Job Shop environment.
- Understand how the “Means” represent a series of interdependent action plans creating a robust approach to Lean.
Lesson 2 | Embrace the 5S’s
- Identify what each of the 5S’s stands for and how it helps an organization reduce waste.
- Understand the tactics/techniques to “sort” by determining what belongs and what does not belong in a work area.
- Explain the rationale for effective storage locations.
- Describe what it means to standardize and why standardization is important.
- Identify strategies to sustain workplace organization and to prevent backsliding.
Lesson 3 | Reduce Set-Up Time
- Describe the purpose and benefits of reducing set-up time.
- Explain the difference between internal and external set-up time.
- Identify the key components of set-up reduction and explain the role each plays in reducing set-up time.
Lesson 4 | Adjust Workflows and Layouts
- Explain the linkage between layouts and workflows.
- Describe why identification of Product Families is an important step for improving layouts and subsequent workflows.
- Understand types of data needed to design effective layouts and workflows.
- Identify major issues for selecting layout and corresponding Macro-Workflow from various options.
- Understand factors to be considered to refine Micro-Workflows.
Lesson 5 | TPM Basics
- Explain how TPM aids Lean efforts and addresses wastes.
- Know the difference between Corrective Maintenance , Preventive Maintenance (PM) and Predictive Maintenance (PdM).
- Understand how the three sequential Phases of TPM build on each other.
- Realize how PdM techniques can further traditional PM practices.
Lesson 6 | The Visual Workplace
- Describe what is meant by the Visual Workplace.
- Understand the meaning of Visual Controls, Prompts and Displays.
- Appreciate how powerful visual aids, supports and alerts can be to make it easer to do things the right way and reduce waste.
Lesson 7 | Track and Improve
- Understand why it is important to measure the progress of action plans.
- Be familiar with potential measures for Lean Job Shop action plans.
Unit 2 Challenge
- An assessment of the learner’s progress in this unit.

4.8 out of 5 stars
Comments from Learners About This Course
- A lot of great content. I really learned a lot. Very in-depth.
- The information presented is direct, concise and pertinent to my job requirements. I enjoyed this course!
You may also be interested in…
- The 5S’s: Workplace Organization – Comprehensive training in the concepts and application of the 5S’s (Sort, Set in Order, Shine, Standardize and Sustain) and how to apply these techniques on the job.
- Mistake-Proofing Training – Comprehensive online training in poka yoke/mistake-proofing techniques for manufacturing operations.
- Gage Training – Comprehensive training in how to use a variety precision hand gages including an overview of basic measuring concepts, introductory blueprint reading, an overview of GD&T, and which gages to use when.