Course Information
Mapping Workflows Training
Learners will be able to:
- Describe key workflow mapping techniques and discuss the benefits of each.
- Use mapping techniques to identify workflow disconnects, hand-offs, and rework loops.
- Improve workflows by eliminating disconnects and reducing hand-offs and rework.
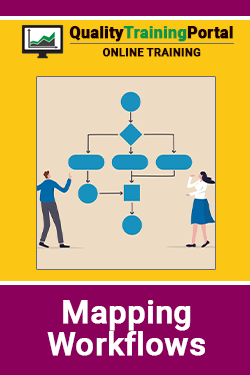
About This Course
Why Map Workflows?
Workflows are patterns of tasks or steps in a process that are designed to lead to an output. The intent of mapping a workflow is to improve a process by uncovering “the good, the bad and the ugly” parts of the process. “Good” steps in a process are value-adding activities. Anything that does not add value is “bad.” Process steps that lead to errors, mistakes and defects represent the “ugly.” With the bad and ugly parts of a process uncovered, it is much easier to identify opportunities for improvement. In a manufacturing environment it is fairly easy to see the physical steps in the process; in an office/service environment steps in the process can be more difficult to see because they include non-tangible items such as information, services or transactions. But there are tools to map both types of processes and that is the focus of this training.
Mapping Workflows Online Training
Mapping Workflows helps employees create visual representations of processes that they work in and provides them with tools that help unveil different aspects of their workflow and see the processes they work in from different angles. By using one or more of the mapping tools covered (Brown-Paper Flow, Workflow Diagrams, Flowcharting, Value-Stream Mapping), learners will be able to identify the causes of nagging problems and take action to remedy them.
IMPORTANT
This course is a great way to learn how to map workflows. It is taken from our comprehensive Lean for Business Processes course. If you have already taken the Lean for Business Processes course, you have already seen the content covered in Mapping Office Workflows.