Course Information
Mistake-Proofing Training
Learners will be able to:
- Describe mistake-proofing effects, outcomes, and solutions.
- Use mistake-proofing techniques to eliminate process and product problems.
- Integrate mistake-proofing into the overall Quality Improvement Process.
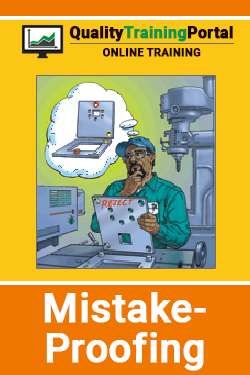
About This Course
What is Mistake-Proofing (Poka Yoke)?
Mistakes seem to happen at the worst time. At work, just before a critical shipment, an inadvertent mistake causes the entire shipment to be rejected. Or at home, just before leaving for a long anticipated vacation, “Murphy’s Laws” intervene, and a series of seemingly unavoidable mistakes delays our departure.
Can we defeat Murphy’s Laws? Can we eliminate these costly mistakes? Probably not totally, but the use of mistaking-proofing tools and techniques will put an end to many of the repetitive, costly mistakes that rob us of time and money both at home and at work.
Mistake-Proofing is more than just incremental improvements or trying harder to do a better job. Mistake-Proofing techniques don’t just reduce the chance of making errors, but they eliminate the possibility for error altogether.
Mistake-Proofing Online Training
Mistake-Proofing online training will help put you on the path to defeating Murphy’s Laws. With Mistake-Proofing, you will not only learn a systematic way to error-proof processes and products, but you will also see a wealth of examples of mistake-proofing solutions applied to real-life recurring problems. Most people learn mistake-proofing skills by seeing examples and then stealing shamelessly to apply similar solutions to their own problems. That’s why Mistake-Proofing is loaded with lots of examples that will trigger implementation of more mistake-proofing solutions in your company. Check out Error-Proofing Support Processes if you are looking for Mistake-Proofing training in a non-manufacturing setting.
Mistake-Proofing is divided into four units. Unit 1, The Mistake-Proofing Primer provides a conceptual background and foundation for mistake-proofing efforts. Unit 2, Effects of Mistake-Proofing, covers practical mistake-proofing techniques. Tools to design and implement mistake-proofing solutions are covered in Unit 3, Mistake-Proofing Solutions. Examples of problems along with accompanying mistake-proofing solutions in a variety of settings are explored in Unit 4, Mistake-Proofing in Action.
- None.
- English (EN-US)
- Chinese (simplified) (ZH)
- Czech (CS)
- French (FR)
- German (DE)
- Italian (IT)
- Japanese (no audio) (JA)
- Korean (no audio) (KO)
- Polish (PL)
- Portuguese (Brazilian) (PT-BR)
- Romanian RO)
- Russian (RU)
- Spanish (ES)
- Vietnamese (no audio) (VI)
Course Objectives
Unit 1 | Mistake-Proofing Primer
- Understand the goal of mistake-proofing.
- Know the language of mistake-proofing.
- Recognize mistake-proofing solutions in everyday life and use these solutions as triggers for ideas to mistake-proof your processes.
- Identify the five process input elements that exist in any process.
- Recognize why errors are made.
- See the value of improving processes so that mistakes are prevented instead of relying on inspection to find mistakes.
Unit 2 | Effects of Mistake-Proofing
- Be able to rank the relative power of the different forms of mistake-proofing effects.
- Recognize a forced control effect. Be able to apply:
- Elimination
- Combination
- Guides
- Process control
- Have an understanding of some of the types of sensors available to achieve a shutdown effect.
- Have an understanding of some of the types of devices available to create a mistake-proofing solution using a warning effect.
- Know how to apply sensory alert effects to mistake-proofing.
Unit 3 | Implementing Mistake-Proofing Solutions
- Learn to apply mistake-proofing solutions after the root cause has been found.
- Be able to evaluate whether the mistake-proofing solution is practical, feasible, and cost-effective.
- Learn how to build-in ways to assure your solution does not get overridden.
- Evaluate the robustness level of your solution.
- Become familiar with 10 improvement tools that complement the mistake-proofing process.
Unit 4 | Mistake-Proofing in Action
In this unit, recurring problems from a variety of industrial settings are explored and successful mistake-proofing solutions are shown. The problems come from the following industrial settings:
- High volume manufacturing.
- Assembly operations.
- A job shop environment.
- Process industries.
- Equipment set-up.
- In the office.
The primary objective of this Unit is to expose you to a variety of mistake-proofing solutions to help you develop your own mistake-proofing solutions.
The secondary objective is to help you think through the solution presented and then identify what type of solution has been used.
Course Outline
Unit 1 Mistake-Proofing Primer
Lesson 1 | What is Mistake-Proofing?
- Rewriting Murphy’s Laws.
- Exploring the source of mistakes.
- The mindset necessary for mistake-proofing.
Lesson 2 | Mistake-Proofing in Everyday Life
- Common examples of mistake-proofing all around us.
- Using these examples to trigger ideas at work.
Lesson 3 | Why Errors Are Made
- How process inputs create process outputs.
- Why the root causes of errors must be identified.
Lesson 4 | Inspecting vs. Mistake-Proofing
- The limitations of inspection.
- Why prevention is always more powerful than detection.
Lesson 5 | How Mistake-Proofing Works
- The language of mistake-proofing.
- The role of teams in mistake-proofing efforts.
Unit 1 Challenge
- An assessment of the learner’s progress in this unit.
Unit 2 Effects of Mistake-Proofing
Lesson 1 | Approaches to Mistake-Proofing
- Exploring the 8 forms of mistake-proofing solutions.
- Guidelines for selecting a mistake-proofing approach.
Lesson 2 | Forced Control Devices
- Delving into the four families of devices and methods used to achieve a forced control effect.
Lesson 3 | Shutdown Devices
- Examining 10 common families of sensors used to achieve a shutdown effect.
Lesson 4 | Warning Devices
- Investigating 4 families of audible alarms and 4 families of visual alarms used to achieve a warning effect.
Lesson 5 | Sensory Alert Devices
- A look at the use of color-coding, missing-in-action clues, and other aids to achieve a sensory alert effect.
Unit 2 Challenge
- An assessment of the learner’s progress in this unit.
Unit 3 Implementing Mistake-Proofing Solutions
Lesson 1 | Integrating Mistake-Proofing and Problem Solving
- How to incorporate mistake-proofing solutions into common problem-solving processes.
Lesson 2 | Practical, Feasible, and Cost Effective Solutions
- Assessment techniques for determining the practicality, feasibility, and cost-effectiveness of your mistake-proofing solutions.
Lesson 3 | How to Keep Solutions from Being Overridden
- Tips for keeping your mistake-proofing solution from being ignored or disabled.
Lesson 4 | How Robust is Your Solution?
- Assessment techniques for determining how robust your mistake-proofing solutions are.
Lesson 5 | Complementary Tools
- How to use ten continuous improvement tools to complement mistake-proofing efforts.
Unit 3 Challenge
An assessment of the learner’s progress in this unit.
Unit 4 Mistake-Proofing in Action
Lesson 1 | Mistake-Proofing in High Volume Manufacturing
- Nowhere are the benefits of mistake-proofing more evident than in high volume operations.
- 8 real-life examples of mistake-proofing solutions in a high volume environment.
Lesson 2 | Mistake-Proofing in Assembly Operations
- Mistake-proofing is a perfect tool to prevent assembly errors.
- 8 real-life examples of mistake-proofing solutions in assembly operations.
Lesson 3 | Mistake-Proofing in a Job Shop Environment
- Mistake-proofing in short-run job shops can make the difference between profitability and bankruptcy.
- 8 real-life examples of mistake-proofing solutions in a job shop environment.
Lesson 4 | Mistake-Proofing in Process Industries
- Mistake-proofing is at the core of complex chemical operations.
- 8 real-life examples of common sense mistake-proofing solutions from the process industry that can trigger ideas to simplify your operation.
Lesson 5 | Mistake-Proofing in Equipment Set-up
- Mistake-proofing is an important element of set-up reduction.
- 8 real-life examples of mistake-proofing solutions to aid equipment set-up and speed product change-overs.
Lesson 6 | Mistake-Proofing in the Office
- Mistake-proofing is not just for plant operations.
- 8 real-life examples of mistake-proofing solutions in the office.

4.6 out of 5 stars
Comments from Learners About This Course
- Good course; used what I learned already.
- Very practical.
- Nice course. Really helped me learn the different types of pokayoke.
- I really enjoyed this training – very detailed with great examples and info for further project planning.
- It helped me with determining which way to go while I’m dealing with an issue or an ongoing issue to help resolve the problem all together.
- The course did a great job at identifying and categorizing different mistake proofing methods.
- I found this course very helpful in understanding mistake-proofing. The content was explained in a clear and easy to understand manner. Many examples were reviewed to provide an understanding of the different mistake-proofing solutions.
- As someone who is working in the Automotive Industry; This course was a great insight into mistake proofing techniques, I loved and enjoyed every minute of it. I will surely be back for more courses along this line.
You may also be interested in…
- Error-Proofing Support Processes – Comprehensive online training in poka yoke/mistake-proofing techniques in non-manufacturing operations.
- 8D Problem-Solving – Step-by-step training in how to work on a problem-solving team follow the 8D methodology including tools and techniques that are used in each step.
- The Five Why’s – Focused training in how to use the Five Why’s technique to get to the root cause of problems.