Course Information
TPM Basics Training
Learners will be able to:
- Describe the value of TPM and explain the benefits of Total Predictive Maintenance.
- Use the three sequential Phases of TPM to improve upon traditional equipment maintenance.
- Calculate and analyze Overall Equipment Effectiveness (OEE).
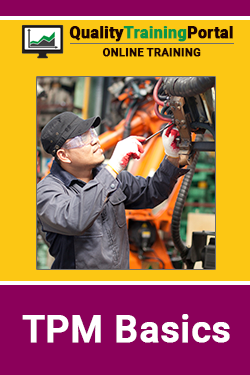
About This Course
Lean organizations strive to reduce waste in all phases of the operation. Some of the least understood and most overlooked sources of waste relates to the condition and maintenance of processing equipment. One premise of Lean Manufacturing is that equipment is ready to run whenever it is needed (to meet customer demands). If the equipment is unexpectedly shutdown in order to be repaired, critical deliveries may be missed. Poor equipment maintenance rekindles the “old” thinking that extra product inventory is needed as an insurance policy just in case process equipment is not operational thereby undermining Lean efforts, adding more waste.
A TPM effort focuses the organization on keeping equipment functioning optimally by reducing the frequency of breakdowns, the need for long, costly rebuilds and by circumventing many equipment malfunctions and intermittent equipment problems. To this end, much of the day-to-day responsibility for routine maintenance is transferred to the person closest to the equipment, the equipment operator.
IMPORTANT!
This Course is Derived from Lean for Job Shops. This course is a great way to learn about Total Productive Maintenance. It is taken from our comprehensive Lean for Job Shops course. If you have already taken the Lean for Job Shops course, you have already seen the content covered in TPM Basics.