Course Information
Process-FMEAs Training
Learners will be able to:
- Conduct a (traditional) Process-FMEA (PFMEA).
- Use RPN results to prioritize risk.
- Create action plans to reduce risks that are unacceptably high.
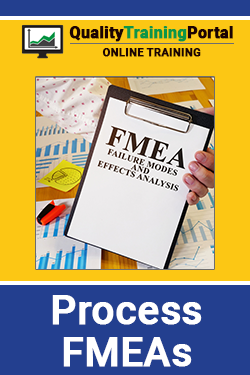
About This Course
What Are FMEAs?
Failure Mode and Effects Analysis (FMEA) techniques have been around for over 70 years. In recent years, use of FMEAs has gained popularity as a quality improvement tool. This interest is in large part due to the automotive industry and specifically its IAFT 16949 supplier requirements. Other major industries, including aerospace, medical products and electronics are also using FMEA techniques as part of their improvement and risk assessment strategies. Unlike many quality improvement tools, FMEAs do not require complicated statistics. FMEA studies can yield significant savings for a company as well as reduce the potential liability of a process or product that does not perform as promised.
Process-FMEAs Online Training
Process-FMEAs training provides step-by-step instructions on how to conduct traditional (RPN) Process-FMEAs (PFMEAs). Learners completing this training will be able to effectively participate on a Process-FMEA team and make immediate contributions to quality and productivity improvement efforts. We also have training on Design-FMEAs, AIAG-VDA Process-FMEA’s and AIAG-VDA Design-FMEAs.
- An understanding of data analysis tools and techniques such as Quality Improvement Fundamentals or the equivalent.
- English (EN-US)
- Chinese (simplified) (ZH)
- Czech (CS)
- French (FR)
- German (DE)
- Italian (IT)
- Japanese (no audio) (JA)
- Korean (no audio) (KO)
- Polish (PL)
- Portuguese (Brazilian) (PT-BR)
- Romanian RO)
- Russian (RU)
- Spanish (ES)
- Vietnamese (no audio) (VI)
Course Objectives
- Explain the purpose of conducting an PFMEA.
- Explain the methodology of the PFMEA process.
- Assemble an PFMEA team.
- Clarify the scope of a PFMEA.
- Work through the 10 steps of a PFMEA.
- Develop custom ranking scales for Severity, Occurrence, and Detection.
- Determine which technology tools to use as aids in your PFMEA action plan.
- Learn how to make the PFMEA into a living document.
- Use the PFMEA establish the basis for a Control Plan.
Course Outline
Lesson 1 | What is an FMEA?
- Know what an FMEA is and why an FMEA is used.
- Understand how an FMEA is conducted works on a conceptual basis.
Lesson 2 | Purpose of an FMEA
- Understand how the systematic FMEA approach getting us to dig into the details of the product or process under study to identify potential risks.
- Realize how an FMEA helps identify risks, prioritizes the risks relative to one another and focuses efforts on an action plan to reduce the risks.
Lesson 3 | Assembling an FMEA Team
- Apply criteria to assemble and effective FMEA team.
- Understand the role of a Subject Matter Expert when conducting an FMEA study.
Lesson 4 | PFMEA Start-Up
- How to define the scope of a PFMEA.
- How to break the study into two or more PFMEAs if the scope is too large.
- How to use a PFMEA Scope Worksheet to clarify and communicate the scope of the study.
Lesson 5 | 10 Steps to Conduct a PFMEA
- Step-by-step directions on conducting a PFMEA.
- Guidance on the use of the FMEA Analysis Worksheet.
- Techniques for customizing the Severity, Occurrence, and Detection Ranking Scales for a PFMEA.
Lesson 6 | Getting More Out of Your PFMEA
- Tips on the best times in a product’s life cycle to conduct a PFMEA.
- Tips on how to use the results of an FMEA to trigger continuous improvement.
Lesson 7 | PFMEA Example
- An example of the application of a PFMEA, working through all 10 steps.
Challenge
- An assessment of the learner’s progress in this course.
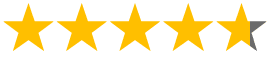
4.7 out of 5 stars
Comments from Learners About This Course
- Excellent with relevant examples to help understand the mechanism of a PFMEA.
- Good description of the flow of steps, and real-life example was helpful to see application of process.
- Provides a basic overview of the PFMEA steps/stages in simple to understand terms, with a real-world example. This helped to put the theory into practice.
- Very well developed and interactive course. I enjoyed the example scenarios and lessons, and can utilize within my organization to improve process methods.
You may also be interested in…
- Mistake-Proofing Training – Comprehensive online training in poka yoke/mistake-proofing techniques for manufacturing operations.
- 8D Problem-Solving – Step-by-step training in how to work on a problem-solving team follow the 8D methodology including tools and techniques that are used in each step.
- Root Cause Analysis with Corrective Action – Leads the learner through a four-step process to get to the root cause (source) of problems to eliminated problems for good.