Course Information
Introduction to FMEAs Training
Learners will be able to:
- Describe what FMEAs are and why they are used.
- Read and understand an FMEA report.
- Use FMEAs to assess and prioritize risk.
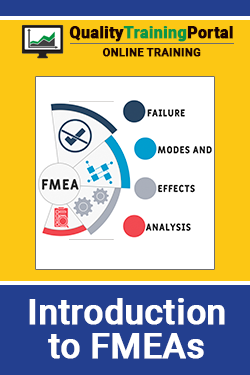
About This Course
What is Failure Mode and Effects Analysis?
Failure Mode and Effects Analysis (FMEA) techniques have been around for over 40 years. In recent years, use of FMEAs has gained popularity as a quality improvement tool. This interest is in large part due to the automotive industry and specifically its IAFT 16949 supplier requirements. Other major industries, including aerospace, medical products and electronics are also using FMEA techniques as part of their improvement and risk assessment strategies. Unlike many quality improvement tools, FMEAs do not require complicated statistics. FMEA studies can yield significant savings for a company as well as reduce the potential liability of a process or product that does not perform as promised.
Introduction to FMEAs Online Training
This online training introduces learners to the basic concepts of conducting a Failure Mode and Effects Analysis. It is ideal for managers and supervisors who oversee teams responsible for conducting FMEAs, but who will not be actually serving on the FMEA team. For more in-depth, step-by-step training see Design FMEAs or Process FMEAs. For the 2019 AIAG-VDA FMEA Methodology, see AIAG-VDA Design-FMEAs or AIAG-VDA Process-FMEAs.